This year’s Nobel Prize in Chemistry is shared by Michael Stanley Whittingham, John Bannister Goodenough and Akira Yoshino. These three world-leading scientists deserve enormous credit for their contributions to lithium ion battery (LIB) technology. The decision to award more than one person correctly reflects the fact that this technology did not appear at once out of the dungeon laboratory of an individual genius, but rather is a history of systematic problem solving.
LIBs have had a huge impact on our society. They enabled modern portable electronics such as laptops and mobile phones. And they are now enabling clean and low-carbon transport, be it via electric cars or even flying taxis, and grid-scale storage of renewable energy.
The success of LIBs is explained by the way batteries work. A battery cell releases the energy from a chemical reaction in the form of electricity. If the internal reaction is a powerful one, this yields a high voltage. And if the materials in the cell don’t claim too much space and are not too heavy either, this gives it a high-energy density in terms of volume and weight.
Lithium is a very reactive element and the lightest metal on the periodic table, so it ticks both these boxes. This is why LIBs rapidly became a crucial part of electronics after their commercialisation in the early 1990s.
Using lithium for electrochemical energy storage is a no-brainer on the back of an envelope. But that very reactivity that boosts the energy content also makes it very difficult to build a cell that can be safely kept in charged state, drained of its energy via electric current, and then returned to charged state just by feeding back that current.
Whittingham took a chance way ahead of time, in the 1970s, by developing and later commercialising (via Exxon) the first lithium-based rechargeable battery. It relied on the compound titanium disulfide (TiS₂), which not only conducts electricity but can also host lithium in its crystal lattice.
If a piece of lithium is placed next to a piece of TiS₂ in a substance known as an electrolyte, the metal will dissolve and charged particles of lithium known as lithium ions will spontaneously move into and stay in the TiS₂. At the same time, electrons are transferred from the lithium metal (the negative electrode) to the TiS₂ (the positive electrode), which allows us to draw a current from the battery.
During the recharge process, the current is reversed and lithium is forced out of the TiS₂ and back to the metal deposit. But one of the peculiarities of lithium is its tendency to form needles and dendrites (long branching structures) during this recharging process. Those can cause internal short circuits, and this made the first generation of rechargeable lithium batteries inherently unsafe.
Goodenough discovered in the 1980s that lithium cobalt oxide was a better alternative to TiS₂ in a LIB. This material contains lithium but is less reactive with its environment and so easier to handle in the manufacturing process. Lithium cobalt oxide became the “father” material of most modern commercial LIBs and powered the first generations of cell phones.
Today, even cutting-edge high-energy electrodes – such as NMC 811 – that boost the range of the next generation of electric vehicles are essentially made from lithium cobalt oxide with the cobalt largely replaced by nickel and manganese in an otherwise similar crystal structure. Cobalt mines are rare and often associated with poor working conditions, so there’s an added advantage in being able to avoid using this metal.
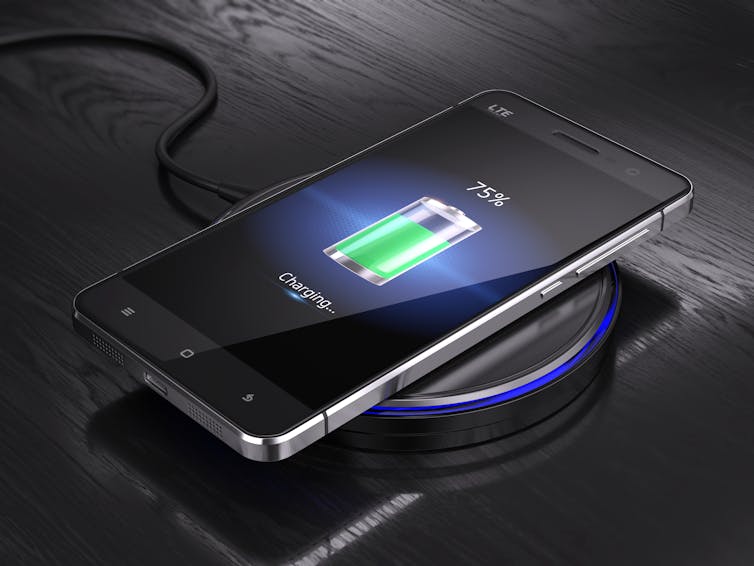
Then in the late 1980s, Yoshino built the first commercially viable rechargeable lithium battery that used graphite instead of metallic lithium as the negative electrode. In this architecture, also used in modern cells, lithium travels between two different host structures: lithium cobalt oxide and graphite. This (in principle) eliminates metallic lithium and so you don’t get dendrite formation.
Yoshino also deserves credit for developing the architecture that enabled the use of organic electrolytes, delivering voltages that are more than twice as large as those with traditional water-based electrolytes. But the poor conductivity of organic electrolytes means the positive and negative electrodes must be thin and placed close together.
Yoshino found ways of coating the active electrode materials on thin metal foils, and was able to to separate positive and negative electrodes by a thin mesh. Only that way could the first generation of LIBs compete with the energy and power performance of the nickel metal hydride batteries that dominated portable electronics in the early 1990s.
Shared success
Goodenough and Yoshino already share the 2014 Charles Stark Draper Prize, which also went to Rachid Yazami and Yoshio Nishi. Those two deserve credit for their findings and inventions that enabled the use of graphite electrodes and that brought LIBs to mass market, respectively.
The success of LIBs also had some indirect helpers which should be remembered in view of future technology commercialisations. In the 1990s, modern microelectronics made it possible to unite video cameras and tape recorders in a single device. Suddenly, battery weight and longevity became product design bottlenecks in a lucrative growing market, which then fuelled demand for LIBs.
At the same time, rewriteable CDs and DVDs were causing the beginning of the end of the audio and video tape business. But the coating processes and the machines used to build the first LIBs were adapted from magnetic tape manufacturing. So it’s not clear if LIBs would have succeeded without that pre-existing manufacturing expertise.
The latest challenge is to scale LIB mass-production from portable electronics to the automotive and energy markets, and this requires concerted global efforts. The three deserving Nobel laureates must surely be happy to see the fruits of their work inspire research projects such as “JCESR”, “Batteries 2030+” and the Faraday Institution. This work has just begun.
Post a Comment